Simulation Results
The COMSOL is chosen for virtual simulation and prototyping, COMSOL is a multiphysics software and it can allow the team to reach the goal to simulate the real working environment of the guidewire. The main reason for the team to choose COMSOL instead of SolidWorks is because COMSOL is more specifically designed for scenarios requiring multiphysics conditions, in this case, the team can better simulate the real working environment of the guidewire inside blood vessels. Figure below shows the model the team created in COMSOL. This version of model is made following the real size because all future simulations will be completed in the software, therefore, there will not be concern about dimension feasibility for 3D printers.

Thermal Test
-
Heat transfer simulation study was conducted on the CAD model using the COMSOL software to verify and validate the group’s design concept.
-
Four distinct domains were established: the guidewire body, the active polymer, the wire, and the surrounding fluid.
-
Materials were defined for each of the four regions which were PLA, Polyurethane, Copper Wire, and blood (simulating inside a human body) respectively.
-
Parameters of each material were used in analysis including the materials’ density, specific heat capacity, thermal conductivity, thermal expansion coefficient, and Young’s Modulus (where applicable).
-
The study was programmed to be laminar flow as this was concluded in past calculations.
​
​
​

Properties of PLA defined in COMSOL
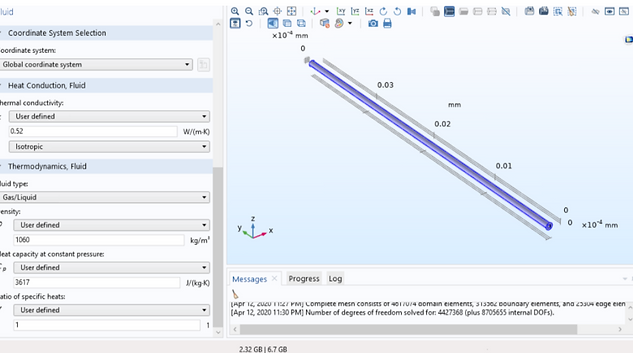
Fluid (blood) properties defined in COMSAL
Stress & Strain Test
Stress and strain tests were performed in COMSOL for the guidewire model. All necessary input data came from previous calculations. Figure below shows a sample input for the stress and strain test.
​
​
​
​
​
​
​
​
​
​
​
​
​
​
Results from the stress test show that the maximum value of stress occurs at the connection part between the conductive wire part and the guidewire base. This result helps the team to understand where the weakest part will be during the operation.
​
​
​
​
​
​
​
​
​
Because the team has not combined thermal analysis and bending tests together yet, the team finished a separate bending test to validate the feasibility of the current structure design. Figure below shows the deformation caused by the fluid drag force in human blood vessels. All required numbers were previously calculated using real-world data.
​
​
​
​
​
​
​
​
​
​
​
​
​
​
​
​
​
​
​
​
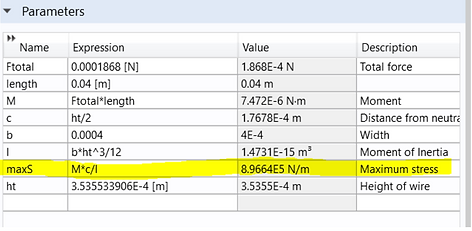


Joule Heating & Electrical System
The team performed a joule heating simulation for the guidewire to verify the conductive wire part will generate heat for the guidewire to deform. The joule heating simulation result shows that the conductive wire will have a stable temperature around 40°C after a certain time, which is our goal because if the temperature increases too much it will cause damage to blood vessels.
A short explanatory video is uploaded below for better displaying the structure and dimension in joule heating simulation:
​​
